Hand operated 3 " Metal Internal key way Cutter .
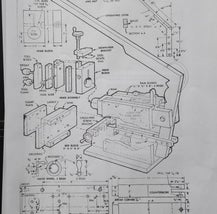
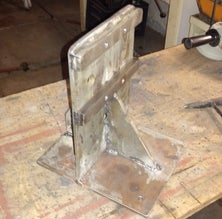
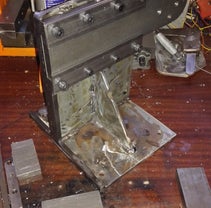
Picture on the left a copy of a hand operated Shaper designed by Mr. S.S Miner in October 1955 this is available on the net. It is now September 2019. This came about being outbid by an individual for a "perfecta " Table Shaper , apparently those Shapers where produced in the UK. I never seen one before and it looked to me to be the ideal tool for cutting key ways in pulleys , gears and that kind of jobs I have decided to Build one myself but will take a few liberties from the original design, all will be recorded on this page.
Picture in the center the body for my Hand operated Shaper made from material that was laying around and will be a big deviation from Mr. S.S.Miners original plans.
Picture on the far right the securing strips made all holes drilled and tapped and the ram fitted temporary to the frame to check it for free movement , a oil hole was drilled on top of the frame and in the center of the ram to lubricate the ram.
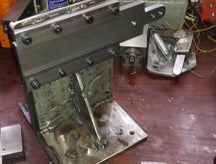
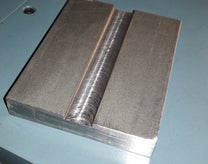
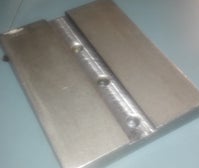
Picture on the left shaped the ram and drilled the holes to take the operating handle, when the handle is made we will have different stroke lengts.
Both picture on the right the head of the ram machined and hole drilled and counter drilled for 6 mm cap screws.
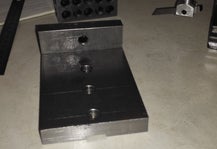
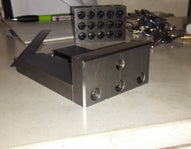
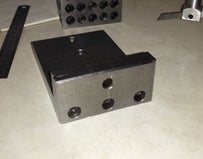
Left and middle pictures manufactured the parts for the tool head of the hand operated Shaper all drilled , tapped the tread for the spindle all ready to be assembled.
Picture far right head assembled with M 6 Allen cap screws.
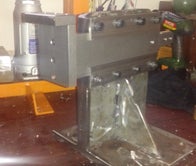
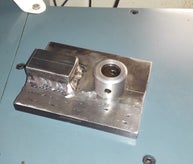
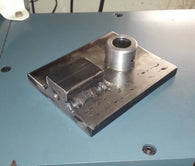
Picture on the left head bolted on to the ram.
Pictures middle and right hand side the sliding tool holder all drilled and tapped ready for the clean up. This tool holder will be fitted instead of the traditional "Clapper"
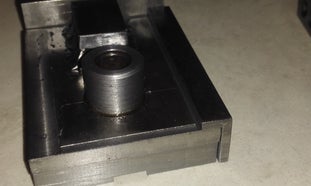
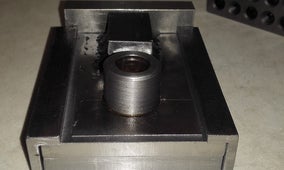
Picture on the left the tool holder all cleaned up and one slide made.
picture to the right second slide made , Ready for the fiholdingnal assembly.
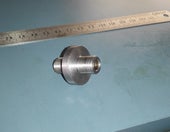
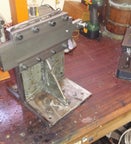
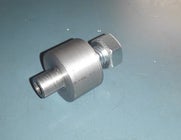
Picture left made a pivot point for the ram.
Center picture pivot point fitted to the ram.
Picture on the right pivot point made to fit on the body so the handle will line up.
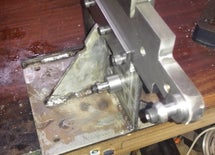

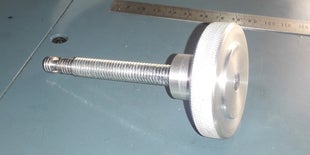
Picture on the left the pivot points made and fitted to the ram and to the body.
Center picture all loosely assembled to take the measurements for the spindle.
Picture far right made the spindle and the turning wheel ready to be assembled.
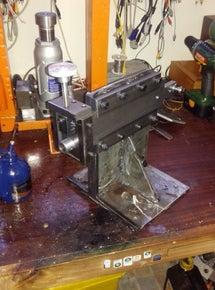
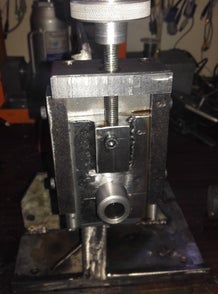
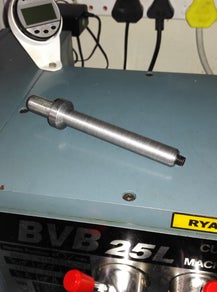
Pictures left and center all the parts of the head assembled and we can move the tool holder up and down quit freely.
Picture on the right hand made a tool holder for the Shaper still have to make a square hole to fit my tool bit drilled and tappet the front m8 and fitted an grub screw to secure the tool bit.
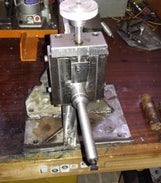
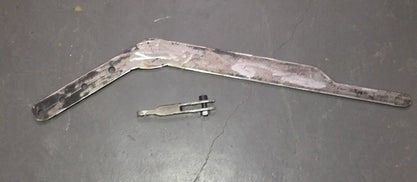
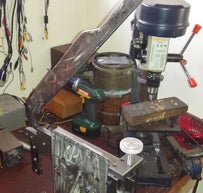
Picture on the left fitted the tool holder to the Shaper . It will make it easy to calculate the overall size I will have to make the table.
Center picture operating lever cut to size and and drilled all the holes together with the bottom link.
Picture far right operating lever drilled and fitted.
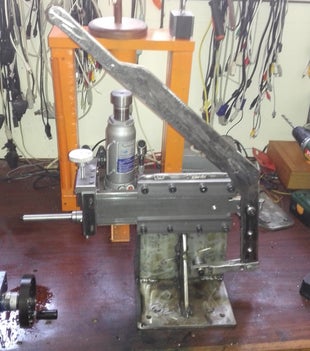
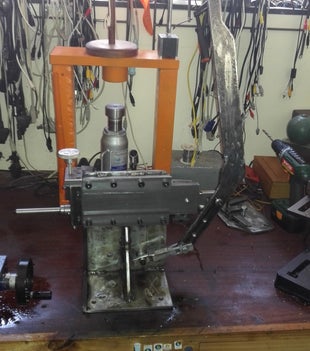
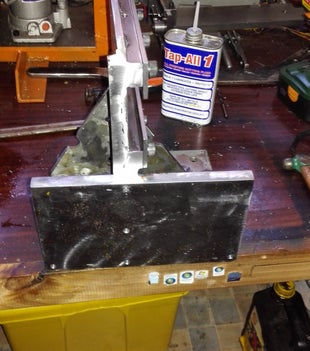
Left and middle pictures a link made and connected to the operating lever this will give a stroke of 90 mm this in turn will give enough information to work out the table size.
Picture on the right 16 mm Face plate made and ready to drill and tap the six securing bolts holes in to the main frame.
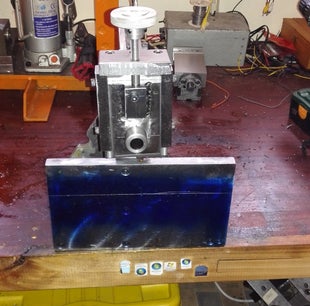
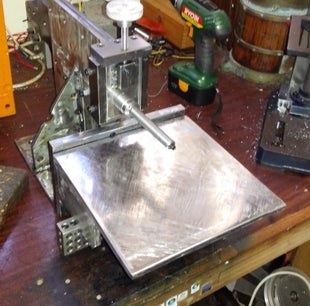
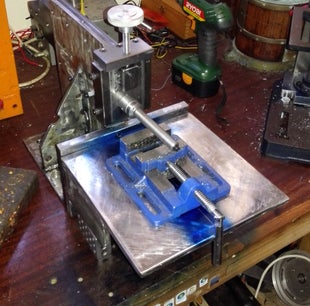
Left all holes drilled and tapped and face plate bolted to the frame the scribe line indicates the height of the table.
Center picture and right hand side picture table made and positioned with one two three blocks.
Picture on the right drilling vice market out and holes drilled and tapped using M 10 holding down bolts.
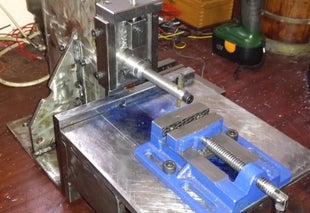
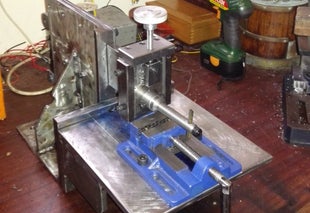
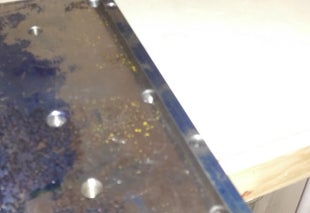
The machine is completed the tool holder was shortened by 25 mm . This gives me a stroke of 95 mm and will have to be tested , the HSS tool bit has to be ground to the correct length, plus the machine has to be bolted down to the table to make it fully operational.
Picture on the right an improvement I hope . I am making the table move on its X axis. starting by bolting a rail to the vertical base plate to vertically support the table.
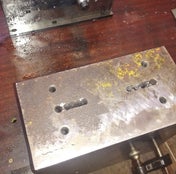
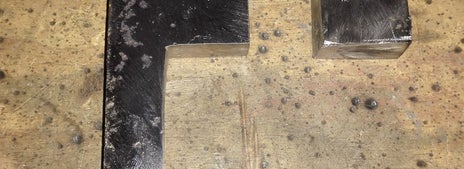
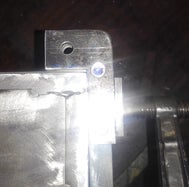
Picture on the left making the slots on the vertical face of the table to give it an 45 mm x axis travel.
Picture in the center the table spindle bracket roughly cut to size made ready to drill and tap all the relevant holes.
Picture on the right spindle bracket all hole drilled and counter sank ready to transfer the holes.
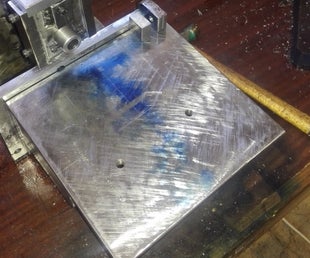
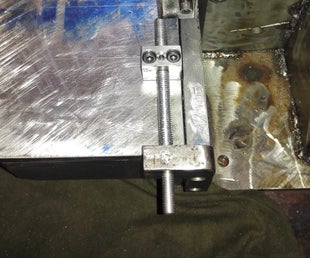
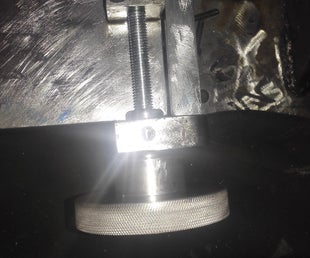
Picture on the left spindle bracket holes drilled ,tapped and bolted to the face plate ready to transfer the spindle bore to the spindle nut which at the moment is sitting loosely on the table surface.
Picture in the center table and table nut drilled and tapped .temporary fitted with spindle cut to size to the table top .
Picture far right hand wheel made and fitted to the spindle.
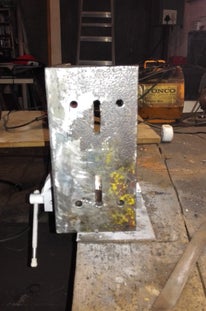
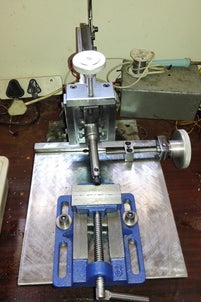
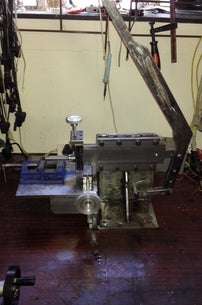
Picture on the left table face plate front slots cut roughly ready to be Cleaned up to take 10 mm x 30 mm Allen cap screws.
Picture in the center the table after assembly moved to the center , this will give me a maximum travel 0f 45 mm from side to side also made four washers under the heads of the four m 10 Allen screws clamping down the table and the vice.
Picture on the right the final product ready to be tested and fine tuned.
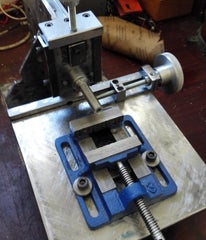
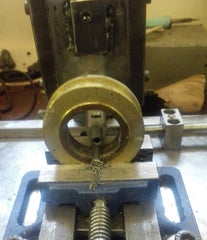
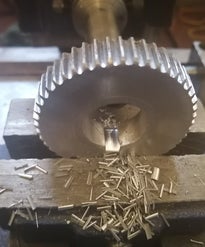
Picture top left small alteration made to the position of the vice I also shortened the tool holder which has still to be machined to the ultimate length and re drilled , and tapped also have the tool holder hole re drilled . I am also playing with the Idea of shortening the table as I don't need such a great overhang , it also reduce the weight al little . Pictures top middle and top right manually cutting a key 5 mm way in a pulley of a home made gear, it is easier than I thought possible .
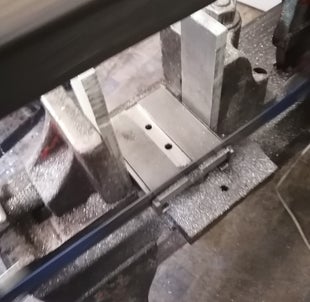
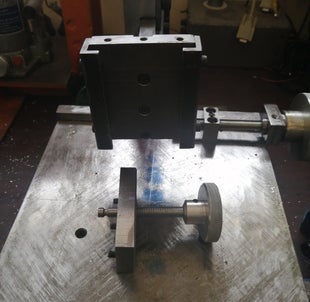
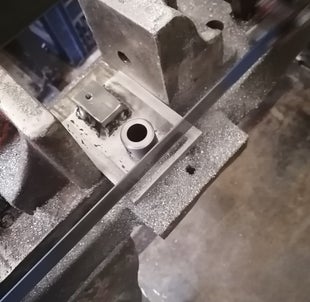
December 2020 some alterations done to the Clapper box , by shortening it using the old power hack saw ,to give more room and be able to cut a key way in the driven pulley of the mini mill. The problem being that the table can only move side ways but is vertically fixed.
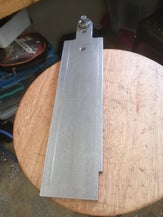
Picture on the left the slide under cut at one side to clear the vice on the horizontal table.
Picture on the right new tool holder made to cut a 3mm key way in a 10 mm bore.
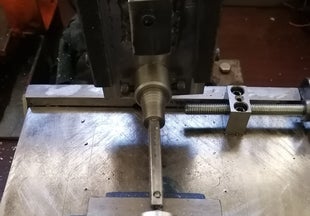
Tool holders Dec 2020.
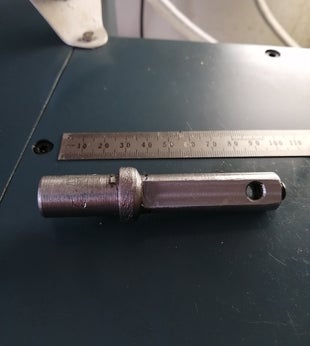
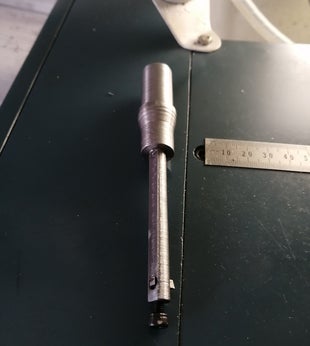
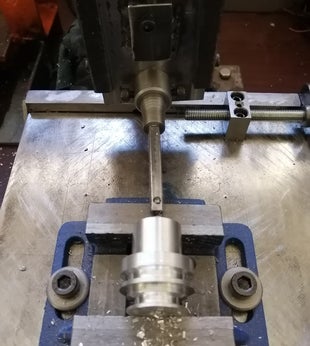
Manufacturing the pulleys for the Mini Mill . I will have to make special tool holders to cut the key ways, see pictures above. One point I want to make is that i milled the top of the tool holders flat in an attempt to give some extra clearance in the bores
Clamping device Dec 2020
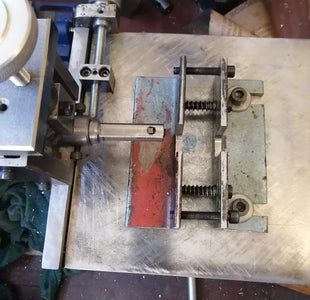
A very simple clamping device for the key way cutter made from left over material of the power hack saw, the angle irons cut to size and slots machined in them . Ready for the holes of the clamping mechanism to be drilled and tapped.
Picture far right all the hole drilled and tapped M8 bolts and springs fitted ready to be tested . I also got a lick of paint to make it look better.
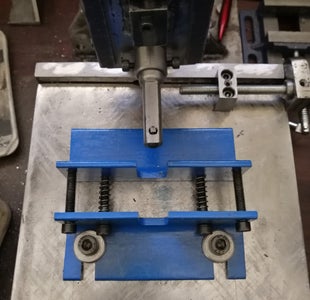
Using the new clamping device. April 2021.
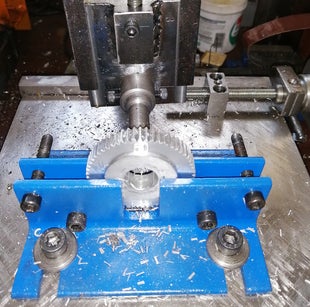
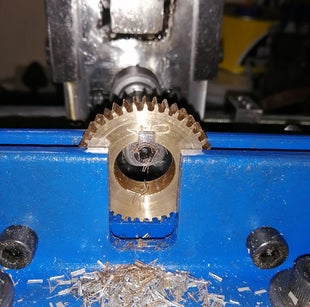
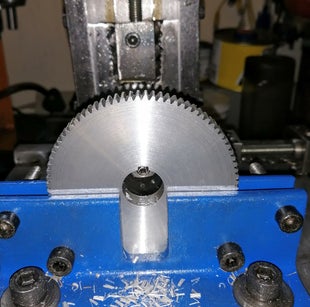
Using the Keyway cutter with the new clamping device succesfully on diverent materials.
Create Your Own Website With JouwWeb