Mini vertical turn table
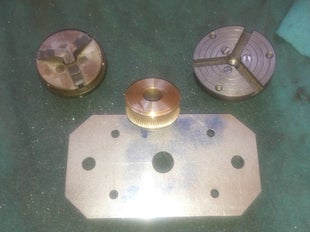
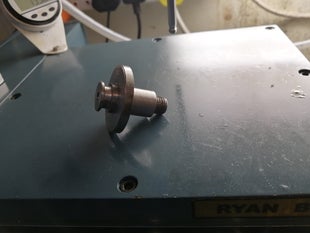
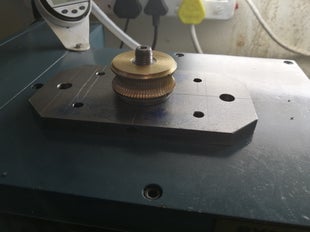
Vertical turn made from material and parts found in the workshop. The chuck and face plate are spare parts of the Unimat SL. The base plate was once part of a milling vice project.
Picture top left the spindle machined ready to press the worm wheel on to the shaft.
The grove machined at the bottom of the shaft will hold the shaft secure to the base plate. The threat used on the top of the spindle is m12 x 1.25
The Bronze worm wheel is left over from the power hack saw project The worm wheel was cut using a M16 x 2 tap. This was done on the lathe.
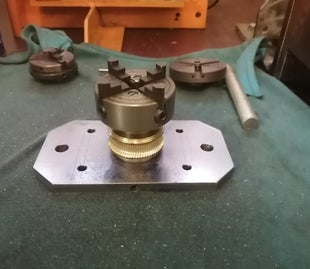
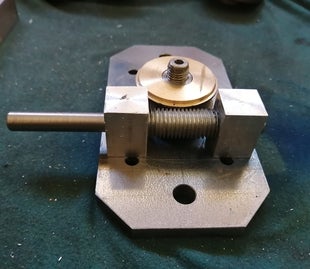
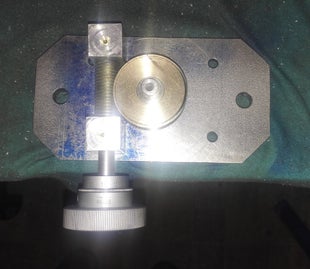
With two set screws. Picture on the top left a four yaw chuck fitted to check it all out. it feels good
Picture in the center , machined down from M16 ready bolt. And two aluminum bearing blocks made.
Picture on the right lube holes drilled in the aluminum blocks on the top and M5 holes drilled and tapped securing the blocks to the base plate. A hand was wheel fitted this was left over of the vertical feed of the milling machine.
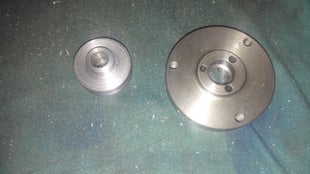
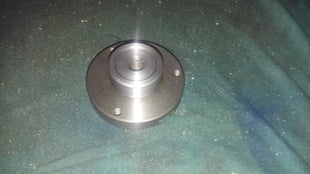
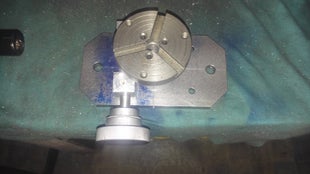
picture on the left adapter for the face plate and three jaw chuck made.
Picture in the center the adapter fitted to the face plate it worked out beautiful, a nice snug fit
Picture on the Top right face plate with adapter fitted to the main body all That has to be done is drill and tap for the securing bolts.
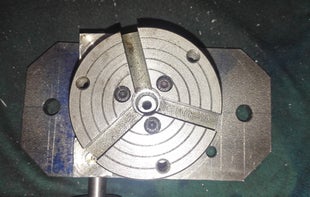
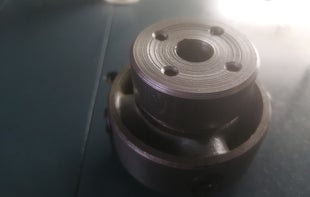
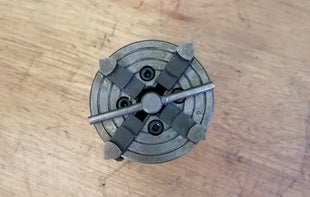
Picture on the top the adapter for the four yaw chuck all drilled and tapped m4 to secure the two parts.
Picture on the right four yaw chuck fitted and ready to be used. The center hole is m12 x 1.25
Some changes Jan 2021.
Made an aluminum surface plate for the turn table 150 diam x 12 mm thick , it bolts on top of the original with m6 x 15 mm counter sank allen set screws .The lines lines are set out on the surface and several holes will be drilled and tapped M6 for easy mounting of future projects.
Picture on the far right all the holes drilled and tapped ready to be used.The holes tapped on the tapping jig to insure they are square.
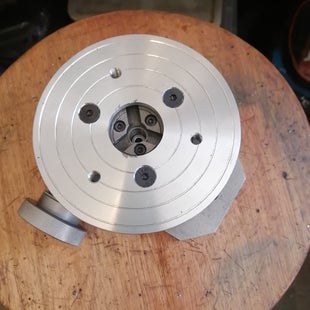
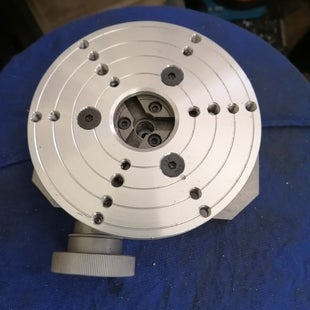
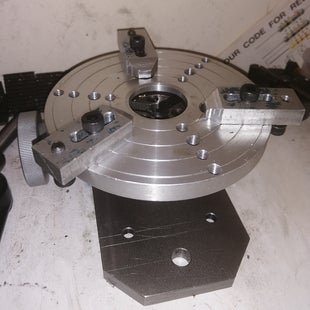
Made an aluminum surface plate for the turn table 125 mm diam x 12 mm thick , it bolts on top of the original with m6 x 15 mm counter sank allen set screws .The lines lines are set out on the surface and several holes will be drilled and tapped M6 for easy mounting of future projects.
Picture in the center all the holes drilled and tapped ready to be used.The holes tapped on the tapping jig to insure they are square.
Picture far right three hold down clamps made and fitted ready to go in to action.
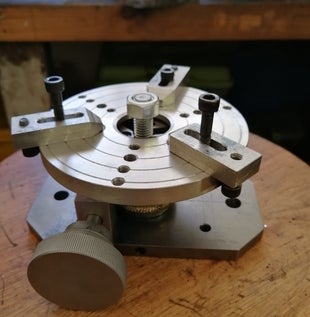
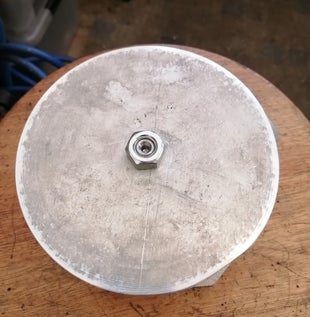
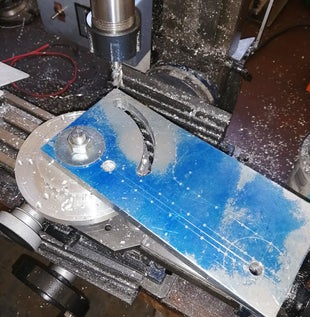
Left top picture M 12 tapped in the center in anticipation of making fraction plates for the dividing head after the design of David . J . Gingery.
A center hole drilled in the center holding down stud to help setting up the mini mill when I start drilling the holes in the fraction plates.
Picture top right the first job done Making a banjo for lathe #2 ,on the turn table it worked satisfactory but there is room for improvement.
Securing the face plate preventing it from unscrewing. March 2021.
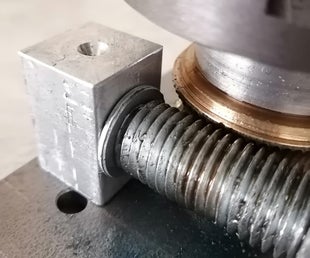
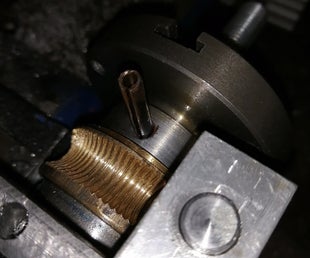
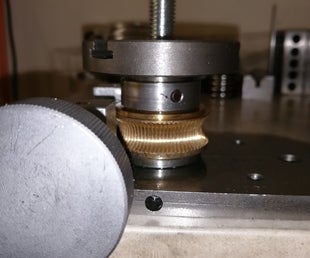
A spacer made and fitted to the worm to take up the slack, also a hole drilled in face plate holder to stop it from unscrewing while in use as happened when we made the Banjo for lathe # 2
Create Your Own Website With JouwWeb