Changes made to the auto feed system . Jan 2021.
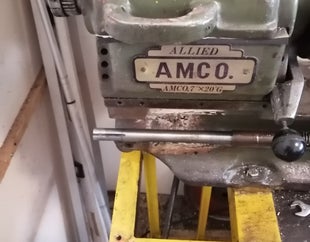
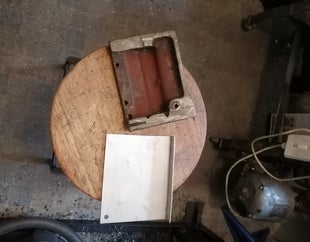
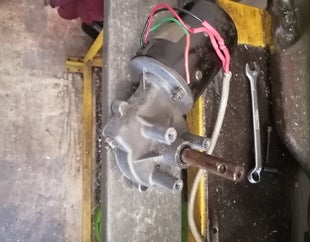
Left top picture the end sprocket and bearing housing removed for the improvement of the auto feed.
Center picture bearing housing cleaned and an aluminum cover made in anticipation.
Picture top right motor removed from its mounting bracket and sprocket removed.
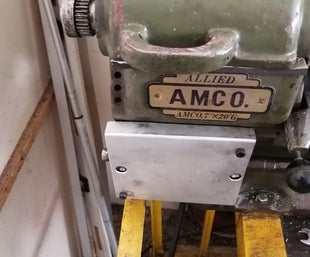
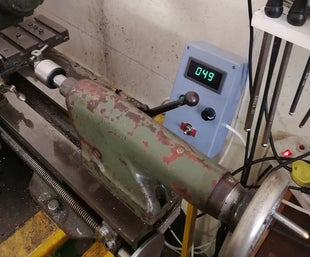
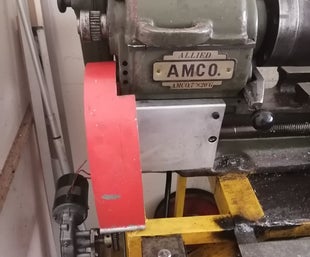
Picture top left the bearing housing refilled , cover plate drilled and tapped and secured also two lubricating holes drilled so the lead screw will be lubricated when in use.
Center picture 12 v motor control fitted so we can regulate the feeding speed, and get a better finish if required.
Picture top right drive motor and chain drive reinstalled and working satisfactory.
Home made main lead screw drive train for a "Allied AMCO 7 x 20 G" lathe
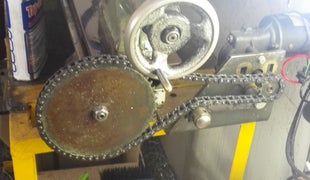
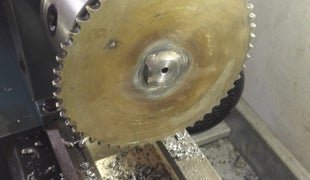
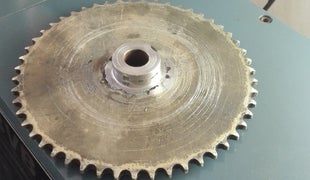
Pictures at the top some time ago I made the automatic lead srew feed drive and it worked satisfactory, but there was one problem it stopped me from removing the tail stock. I found an other identical sprocket , welded a round bit of stock to it and machined it to fit on the opposite side of the feed shaft.
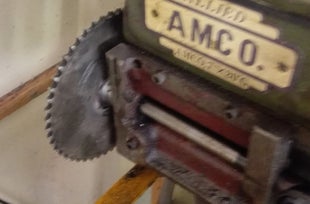
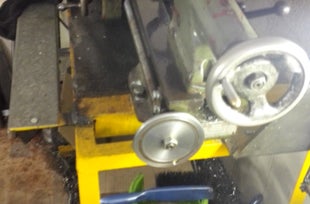
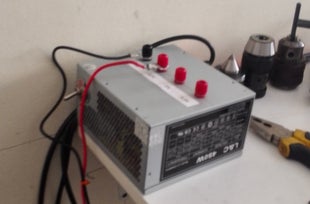
The next set of pictures show the new sprocket being temporary fitted ,while I machined down the original to a diameter of 90 m/m to make a hand wheel out of it, I also drilled and tapped a M8 hole in it to maybe fit a handle on that wheel should I ever need it. The drive motor has also been removed , and will be installed under the main sprocket nicely hidden at the back of the lathe , a bonus the Tail stock can now be removed, if I want to use the Steady that I am in the process of manufacturing.
Picture on the far right the converted ATX 12v power supply to be used to drive the lead screw motor.
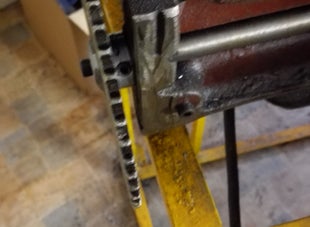
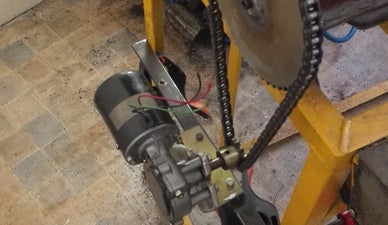
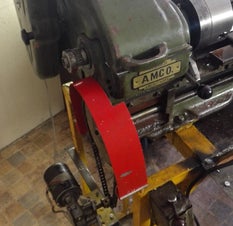
Picture top left sprocket ID machined to tight sliding fit , then permanently fitted to the feed shaft. Sprocket is secured with a M8 grub screw, a m6 hole was drilled in the centre of the shaft and a m6 x 20 hex cap allen screw was fitted.
Picture top centre mounting bracket of the drive motor , cut down and to be in proportion with the rest of the installation and temporary clamped in to place waiting for the mounting holes to be drilled.
Picture top right all wired up and ready to go for safety sake a guard was fitted over the exposed chain drive. The guard was mainly fitted over the drive chain because the main On/Off switch is situated in that position and could be dangerous for busy fingers
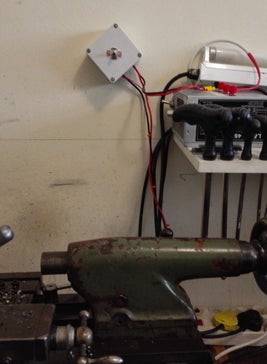
Left picture fitted a double pole double trow switch in to the feed system, now it is possible to run the automatic feed in either direction, which may come in handy in the future. It also adds the possibility to trow the switch in to the center position and stop the feed if the need arrives.
Compound and tool post.
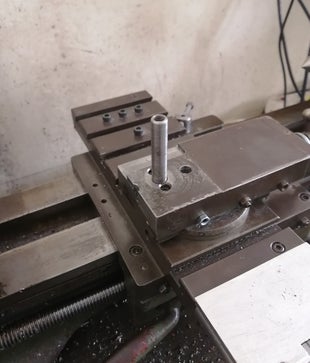
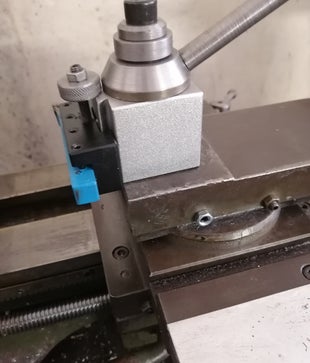
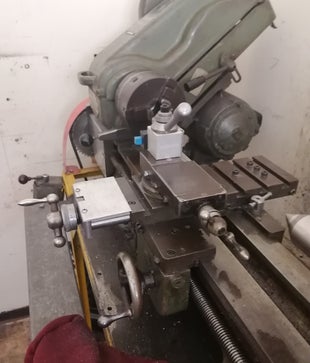
Above Pictures compound cut shorter by 12 mm to make the tool holder fit properly as can be seen in the picture.
Create Your Own Website With JouwWeb